Внедрение «1С:WMS» на «Альметьевском трубном заводе» позволило добиться экономического эффекта на 5,8 млн рублей в год
Автоматизация на базе «1С:WMS» больших складов и крупных производственных предприятий – задача сложная и трудоемкая. Однако все затраты на проведение такой автоматизации при грамотной реализации проекта окупаются. Сегодня мы наглядно продемонстрируем это на примере «Альметьевского трубного завода», успешная автоматизация склада которого позволила добиться экономического эффекта на более, чем 5,8 млн рублей в год, то есть все затраты на реализацию проекта внедрения WMS-системы окупились в первый же год.
Исходная ситуация на предприятии
«Альметьевский трубный завод» (в настоящее время является филиалом АО «ВМЗ» и входит в состав «Объединенной металлургической компании») – один из крупнейших в Поволжье производителей стальных электросварных труб с высококачественным наружным покрытием. Специализируется на выпуске труб малого и среднего диаметра для нефтегазопроводов, водопроводов и систем отопления, также выпускает квадратный и прямоугольный профиль для строительства и других отраслей. Годовой объем производства продукции – более 200 000 тонн. Всего на заводе работает около 700 человек, 80 из которых являются сотрудниками склада. Общая площадь всех складских площадок предприятия составляет 83 460 кв.м.
Завод долгое время работал без единой автоматизированной системы управления складом. Это приводило к возникновению целого комплекса проблем разной степени критичности:- контроль приемки, хранения и отгрузки готовой продукции осуществлялся вручную, большая часть операций велась на бумаге с последующим внесением данных в зарубежную ERP-систему, что негативно отражалось на скорости работы;
- размещение готовой продукции в специальные «карманы» на складе происходило по наличию свободного места (не систематизировано), что в дальнейшем негативно отражалось на скорости отгрузки;
- точное место хранения номенклатуры не фиксировалось и было неизвестно – у работников склада уходило до 1,5 часов только на поиск нужной продукции при комплектации заказов, что резко негативно отражалось на скорости отгрузки;
- из-за недостаточности данных и трудоемкости ручного контроля не было возможности соблюдать принцип FIFO, вследствие чего возникали потери из-за перевода труб в пониженную сортность.
Решить все перечисленные проблемы и существенно повысить эффективность работы предприятия позволяло внедрение «1С:WMS». За реализацию проекта внедрения от начала и до конца отвечали специалисты компании «СИТЕК», являющейся официальным разработчиком данной системы с 2018 года и сертифицированным партнером фирмы «1С».
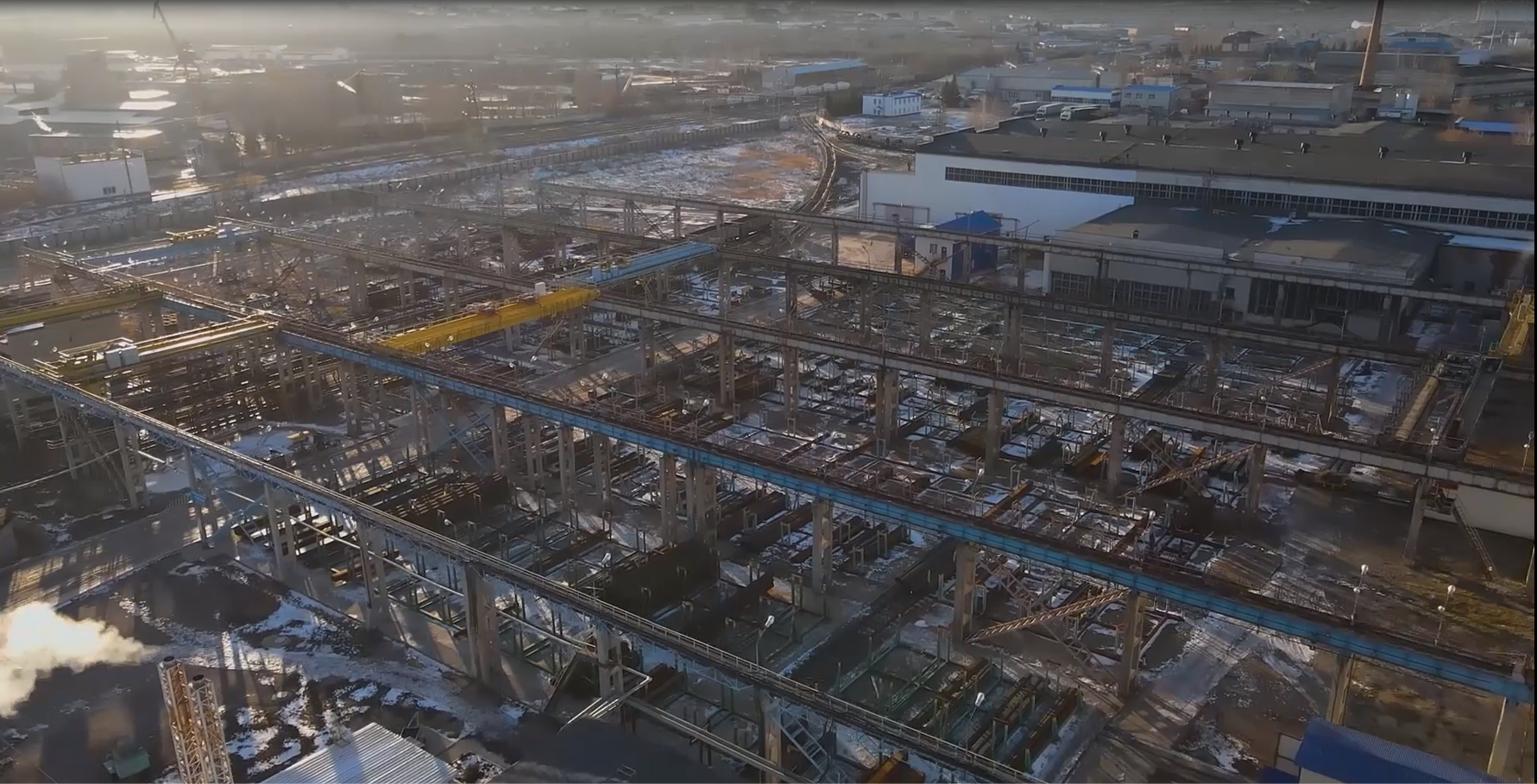
Особенности проекта
Уникальность проекта автоматизации «Альметьевского трубного завода» обусловлена спецификой предприятия: разделенная складская зона, хранение продукции в специальных «карманах», приемка и отгрузка продукции с указанием характеристик не только конечного продукта, но и материала, из которого он изготовлен, а также особый контроль вывоза продукции с территории завода.Общая территория склада завода имеет сложную структуру. Она разделена не несколько взаимосвязанных зон, между которыми постоянно происходит движение продукции, при этом в структуре имеются как открытые, так и закрытые склады:
Наименование: | Емкость склада, т | Площадь склада, кв.м |
Закрытые склады | 13100 | 20424 |
Закрытый склад продукции СГП-3 ТЭСЦ-2 | 8500 | 9400 |
ТЭСЦ-1 (внутренние закрытые площадки) | 3600 | 2600 |
ТЭСЦ-2 (перекаточная галерея) | 1000 | 8424 |
Открытые склады | 31500 | 63036 |
Склад готовой продукции ТЭСЦ-1 | 11500 | 19836 |
Склад готовой продукции ТЭСЦ-2 | 20000 | 43200 |
ИТОГО (закрытые + открытые склады) | 44600 | 83460 |
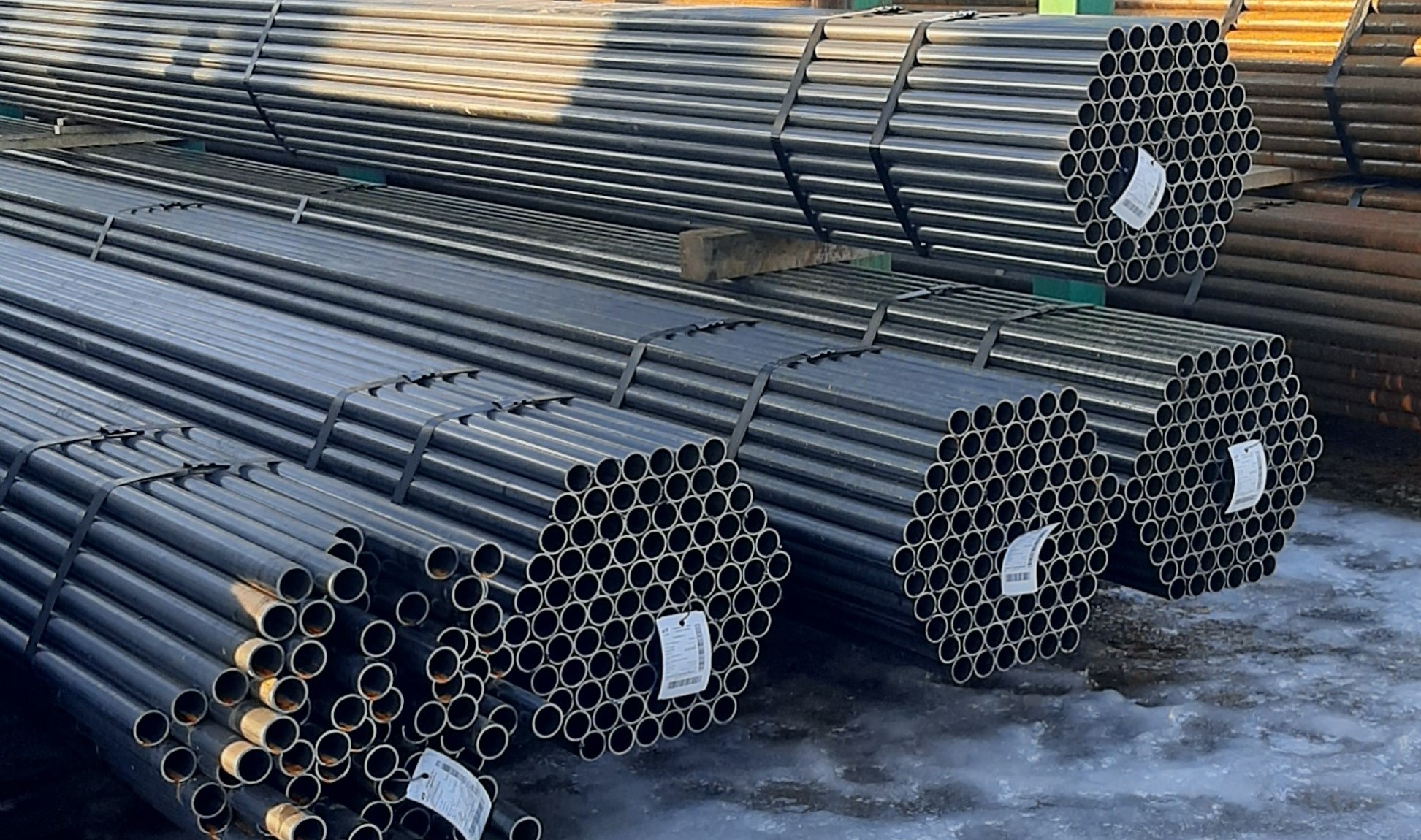
Что же было сделано?
На первом этапе специалисты «СИТЕК» разработали функциональную модель внедряемого решения. Были определены:- порядок зонального деления и топологическая модель склада;
- правила и стандарты работы с применяемыми на складе системами хранения;
- правила и стандарты работы сотрудников склада;
- порядок выполнения операций приемки, размещения, отбора и отгрузки;
- порядок выполнения операций внутреннего сервиса;
- правила и стандарты подготовки продукции к отгрузке.
Выполнена комплексная доработка функционала «1С:WMS» по требованиям заказчика. В частности, реализован пакетный учет с автоматической маркировкой контейнеров («подъемов») продукции.
Выполнены доработки в части непрофильных для WMS функций учета производственных переделов (изоляция, термообработка, ремонт, перемаркировка продукции).
Выполнены работы по систематизации признаков продукции для «Отбора при отгрузке клиенту», значительно доработан функционал системы под отбор продукции на каждую строку полученного требования отгрузки. С учетом данных признаков производится автоматический отбор продукции на складе, что позволяет сократить трудозатраты сотрудников склада на поиск.
Осуществлены значительные доработки WMS в части адаптации процесса инвентаризации к требованиям используемой зарубежной ERP-системы, разработаны 12 интеграционных сценариев с различными ее модулями.
Внедрение и использование на предприятии ТСД (терминалов сбора данных) позволило автоматизировать операции приемки с производства, внутренних перемещений и отбора продукции, практически полностью отказавшись от «бумажной работы». Также с помощью ТСД сотрудниками охраны оперативно осуществляется заключительный контроль вывоза продукции с территории завода в полном соответствии с внутренними правилами безопасности.
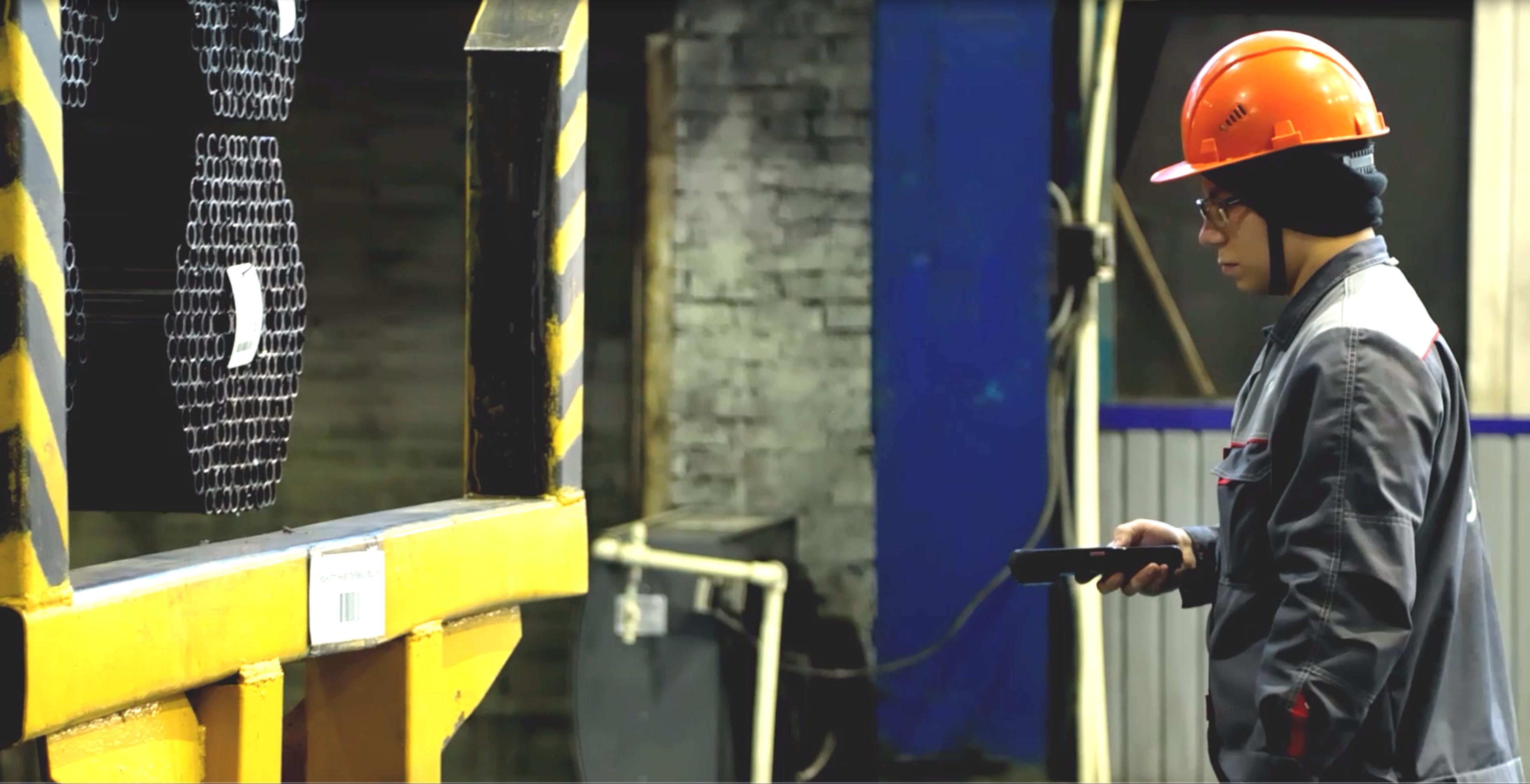
Всего автоматизированы и настроены следующие функции:
- управление складскими запасами;
- логистика адресного склада;
- контроль и учет серийных номеров, сроков годности и сертификатов;
- анализ запасов ABC/XYZ.
- выполнена интеграция «1С:WMS» с зарубежной ERP-системой по различным модулям;
- разработано рабочее место «Приемки из производства» с функциями фиксации данных о качестве производимой продукции;
- разработана подсистема для возможности оценки качества производимой продукции;
- реализован индивидуальный и пакетный учет труб;
- планирование продукции с учетом дополнительных требований, задаваемых менеджерами;
- новый механизм оценки заполненности ячеек;
- централизованный механизм проведения плановых инвентаризаций;
- организована работа с несколькими складами в одной базе;
- контроль движения продукции на посту охраны;
- учет индивидуальных кодов маркировки на весовом товаре;
- переработан стандартный интерфейс «1С:WMS» для удобства работы с трубной продукцией;
- разработана новая подсистема для маркировки продукции составными штрихкодами;
- минимизировано количество операций ввода данных для выполнения задач.
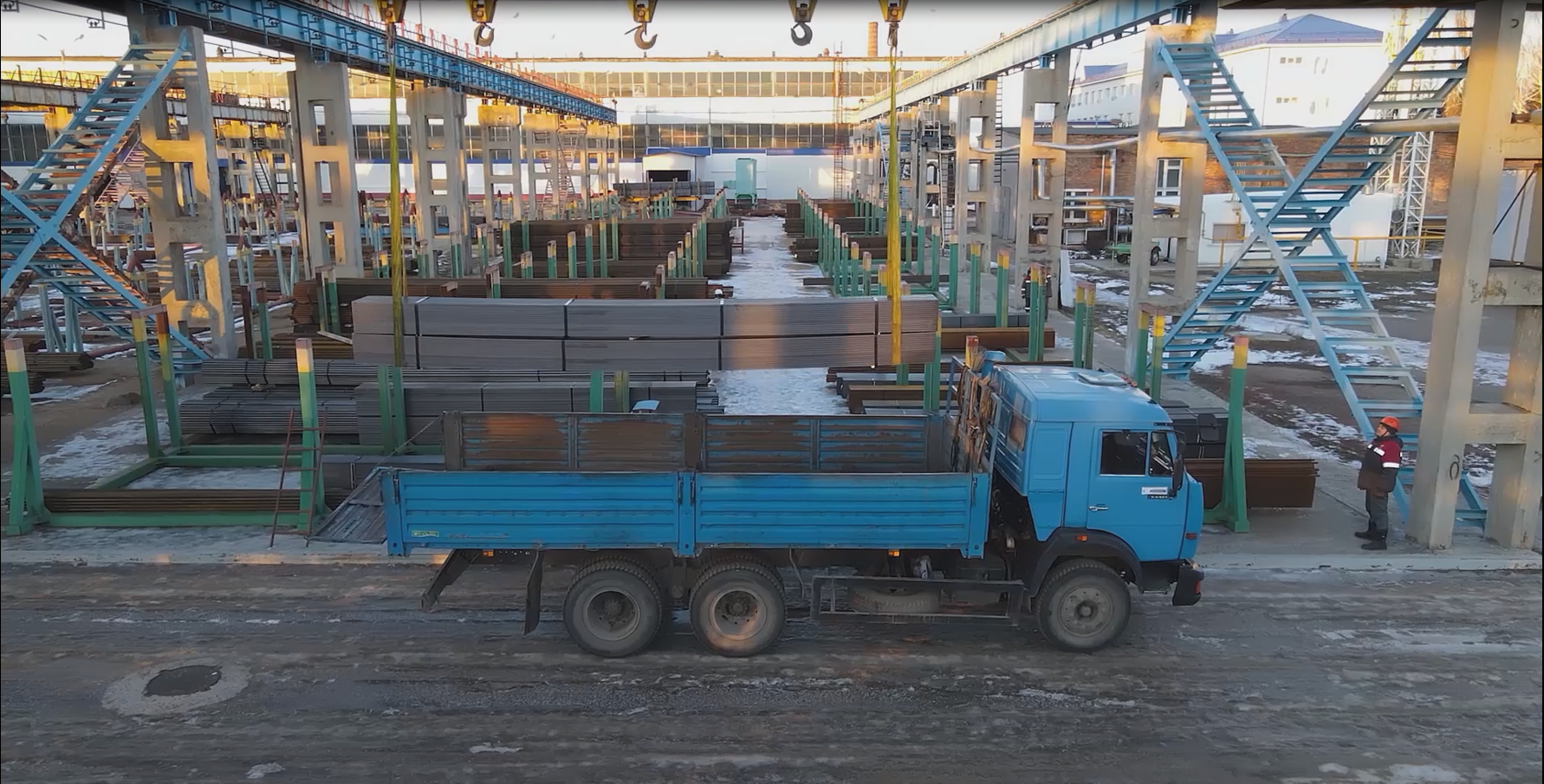
Итоги проекта и экономический эффект
Полностью настроенная и доработанная система «1С:WMS» участвует во всех процессах: от производства до выезда готовой продукции с территории завода. В ходе реализации проекта на складе завода было автоматизировано 39 рабочих мест и обучено 4 смены сотрудников (более 60 человек), которые непосредственно взаимодействуют с системой – для них разработаны необходимые правила и инструкции.Благодаря внедрению системы, на предприятии были структурированы остатки, обеспечивается оперативный и прозрачный учет продукции, автоматизирован контроль качества выпускаемой продукции, соблюдается принцип FIFO. Категорийное управление ассортиментом и организацией хранения, поддержание неснижаемых товарных запасов по ключевым категориям и позициям позволило заводу добиться существенного сокращения объема замороженных средств, связанных с порчей товаров и хранением сверхнормативного запаса продукции.
Внедрение «1С:WMS» позволило улучшить клиентский сервис и снизить риск потери текущих клиентов из-за недостаточного качества сервиса отгрузки – с момента внедрения системы оценка клиентов по сервису обслуживания улучшилась, завод стал более конкурентоспособным. Кроме того, увеличилась пропускная способность склада за счет увеличения скорости отгрузки и, как следствие, появилась возможность обрабатывать большее количество заказов в день. Данный фактор также позволил повысить удовлетворенность клиентов и повысить конкурентоспособность предприятия.
Экономический эффект от внедрения системы составил 5,875 млн. рублей в год:
- оптимизация среднего сверхнормативного запаса продукции (до проекта на заводе отсутствовала подробная аналитика, которая бы помогала принимать управленческие решения о сезонном накоплении труб, не было данных о времени хранения готовой продукции в разрезе партий и категорий оборачиваемости) обеспечила эффект в размере 1% от общего сокращения сверхнормативных запасов – 1,384 млн. рублей;
- сокращение стоимости грузообработки и хранения (снижение стоимости обработки и хранения 1 тонны готовой продукции с 323 рублей до 250 рублей) обеспечило эффект в размере 4,491 млн. рублей.